In safety footwear, except for basic models, which are entirely outsourced to manufacturers located in China, and which represent a small part of total revenues, the Group controls the entire value chain according to a vertically integrated business model, with a workforce of approximately 4,400 employees.
Design & Development:
The Group's R&D activities are carried out at the two Italian facility located in Trani (BT) and Paruzzaro (NO) and are oriented both to the research and identification of raw materials, production materials and components and to new production techniques capable of improving and enhancing the quality and technological standards of the products.
The development of the models takes place in several phases that start from the design and creation of prototypes, to move on to the creation of a sampling, which is subjected to quality control and compliance tests with the reference standards, up to the final version of the items.
The ability to innovate and develop safe and technologically advanced products represents the strength of the Group's strategy, which then directly manages the production in the plants located in Tunisia and France.
On the other hand, as regards the Basic lines of protective footwear and workwear, the Group uses selected, coordinated and periodically verified Asian manufacturers.
Production:
The main production plant, located in Tunisia, is a state-of-the-art facility that covers an area of 100,000 square metres with a local workforce of about 4,200 employees who produce the medium / high-end lines, equal to approximately 87% of the production.
The Group also has a commercial and production facility in France (≃ 6% of production), while the production of the basic lines of protective footwear is outsourced to selected Asian manufacturers (≃ 9% of the total product).
As regards technical workwear, the Group manages R&D, industrialization and marketing activities, while production is outsourced to manufacturers located in APAC countries.
Marketing:
U-Power Group markets its own brand products and, to a lesser extent, third party brand products (Private Label) through B2B sales.
The customers of the Group are mainly represented by small and medium-size retailers such as hardware stores and shops specialized in the sale of work items, through which the products reach the end user (artisans, small entrepreneurs, workers of medium-large and large companies), mainly in the European market.
Sales take place mainly through sales agents in contact with a large network of distributors and resellers.
PRODUCTION CHAIN:
The design process is entirely managed in Italy by a dedicated team that develops about 500 new prototypes every year starting from careful market analysis that involves:
01
Examining adjacent markets, such as sportswear and outdoor apparel;
02
Pull marketing, promoting the product across a wide base of loyal customers (but not just them) to increase demand;
03
Dedicated sessions with technical material suppliers;
04
Marketing Intelligence for a greater understanding of the market, competitors and end users’ needs.
The time required for this first design phase is approximately 3 months. The production ramp-up phase starts with the top part of the shoe: the upper. The design of the upper is based on the new model to be made and obviously depends on the product’s sales budget.
The steps and times required are as follows:
01
Industrialisation of the upper – 4/6 weeks;
02
Production of the upper – 4 weeks;
03
Injection and finishing – 2 weeks.
Meeting all the regulatory requirements is essential and involves a certification process that also includes the dimensional curve of the mould; this is then followed by international design/patent registration procedures.
The timeframe and launch of the new product onto the market involve various areas, including production and distribution capacity, the international effort of the sales force, the logistics capacity and, last but not least, any active marketing and communication strategies – television, the press (newspapers and magazines) and social media networks.
The two logistics sites in Italy and the UK allow for swift, smart distribution that can quickly meet the requirements of approximately 7,600 customers in Europe. The products reach the end customer through special distribution channels for each local market: national distribution chains and independent distributors.
Technological innovation:
The majority of strategic development is based on research that aims to increase and improve products. The starting point is designing high-tech, high-quality models that take into account not only comfort and safety requirements, but also health protection issues and the risks around musculoskeletal disorders due to repetitive positioning and movement during work.
The attention is therefore focused on creating a high-quality product that can actively help workers’ well-being and pays constant attention to social/environmental issues.
The design and study of trends are priorities in conceiving and creating new concepts and models.
The preliminary study is increasingly focused on in-depth analysis of work stations and processes, analysed in terms of ergonomics.
This means that, alongside aspects linked to safety, it also takes into consideration the primary conditions and issues which workers can find themselves having to address while doing their job, in order to offer them increasingly high-performance and effective solutions to ensure their well-being.
Research and development represents a key factor in the Group’s success and the two Italian centres in Trani (BT) and Paruzzaro (NO) are constantly committed to researching into new raw materials, materials, parts, new production systems to improve efficiency and quality standards, to eliminate product defects and to offer an end product that is increasingly aimed at relevant geographical target areas and production sectors – industry, agriculture, the third sector and respective submarkets by their nature and type of business.
When conceiving and launching the design process, the Group also estimates the costs, potential revenue and investments required to develop the new product, taking into account the performance of the relevant market and analysis of the main competitors.
The Group then develops a technical feasibility study to finalise the project or to customise it by working on the aesthetic side.
The Group then develops a technical feasibility study to finalise the project or to customise it by working on the aesthetic side.
The success of R&D is measured by the group’s capacity to develop the most cutting-edge technologies before its competitors as well as products in line with the most advanced industry standards in order to patent its products and to protect them through industrial and intellectual property rights.
U-Power Group’s investments in brand awareness, and particularly for U-Power, have increased awareness of the brand by improving its reputation.
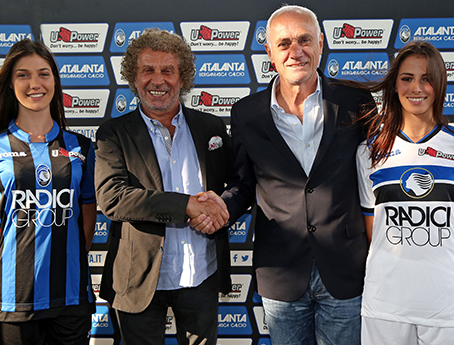
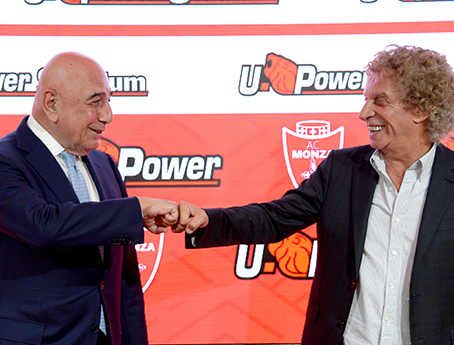
The Group’s current financial commitments, equal to €11.5 m in 2020 with a CAGR 18-20 of 13.2%, are primarily focused on the Italian market, but the goal for the future is to develop a targeted marketing and communication strategy in other European countries too.
U-Power’s advertising reach stretches across Italy, France, Spain and Germany.
In terms of the Italian market, the current strategy is applied in various areas: The media, the press (newspapers and magazines), social media networks and sponsorships, also including theatres, radio and the biggest newspapers.
An outstanding brand ambassador, the famous TV presenter, Diletta Leotta, who is the new face of U-Power;
New and ongoing TV campaigns broadcast on Mediaset networks and other international channels;
Technical sponsorship of the DP19 Yamaha motocross team;
Main sponsor of the U-Power Racing Team, which competes in the rally championship;
Sponsor of AC Monza Club from summer 2020 and naming rights for the U-Power Stadium;
Former sponsor of Atalanta BC (who play in the Champions League).
Except for technical workwear, which is entirely outsourced to Asia, and low-margin basic protective footwear, which accounts for 7% of the total, all our products are made at the factories located in France and Tunisia..
U-Power Group can produce products and technologies intended for various applications at these factories, sharing the technological solutions developed across the board.
The main production plant is in Tunisia, formed of a cutting-edge facility that covers over 100,000 sqm with 4,197 local employees at the end of 2020 and run by 21 European managers and office staff to ensure the highest efficiency and that high quality standards are met.
The factory in Tunisia covers about 87% of the Group’s entire production, accounting for approximately 16,500 pairs of safety shoes, while the factory in France, which is second in terms of importance, roughly covers the remaining 6% of production.
The French factory is used for the final part of the production process, i.e. assembling the layers and soles with the semi-finished uppers made in Tunisia.
In late 2020, it had 22 workers and 44 managers and office staff, with daily production of approximately 1,200 pairs of safety shoes, accounting for roughly 7% of the Group’s entire annual production.
The plant in Tunisia is divided into two production areas. The first one produces the upper and assembles them together with the soles; the second one produces certain semi-finished parts such as the toes and insoles.
The production units for the uppers primarily work on folding and stitching lines, which differ depending on the operations required to create the various upper models; while the upper and sole assembly unit mainly works in injection manufacturing cells.
When necessary, the Group can always open up new production lines and increase shifts on existing lines. Once the assembly phase is finished, the quality control, testing and efficiency phase for the production process begins.
This phase of the process also includes waste management, maintenance of the plants and machinery used for production, the repair of potential faults and the constant improvement of production processes by monitoring production, actual production capacity and real productivity.
This system lets the Group check the proper adjustment of its production machines, the compliance of its products with existing regulations and the successful result of tests required for European certification in accordance with European Directive PPE 89/686/CEE.
01
The sole’s puncture resistance;
02
The toe caps’ impact and crushing;
03
The dissipation capacity;
04
The soles’ grip;
05
The resistance to repeated bending;
06
The soles’ abrasion resistance;
07
The tear resistance;
08
The heel’s energy absorption capacity;
09
The slip resistance.